Introduction: Micro Coal Forge
Hello world...
For many days I have been thinking to start metal working.... Like making small jewellery, tiny metal swords and many more... For these works... It's handy to have a forge... It can be a gas forge... Or it can be the traditional coal forge... I do have small gas blow torches.. But... I wanted a proper forge... And after procrastinating for a very long time... I finally decided to make one.. Now... I didn't wanted to make a full size forge.. Because I don't have enough space to store it.. And the need of a full size forge... It's just for getting started...
So I made this 'Micro Coal Forge' from some already existing item... (I'm not counting the 3d printed blower 😂)... You can get a manual blower for under 3 $... My whole project costes me like under 5$..(yes.. Including the coal)
So without procrastinating longer... Let's gets stared to the build process....
Step 1: Things We Are Going to Need...
Essentials
Paint can / any other can
Fine sand
White cement + plaster of Paris
Cement
Metal pipe
Small nuts and bolts
Large nuts and bolts
Metal hinges
Air blower
Coal
Extra / better if available
Ceramic fiber blanket sheets(take proper health protection)
Good quality air blower (I made mine... You may buy one)
Items according to you.. Which you may use to improve the forge...
For this project i didn't made any plans or files... As it's just a showcase of unplanned budget build... I may have made a proper plan and template files.. If I was building a bigger or proper forge... This version is enough to get started with whatever materials you have lying around in your workshop...
Step 2: Preparing the Metal Can
The very first step of this project is getting a clean metal can.. I have used a empty paint can... But you can use any other type of metal can... (I did paint the can.. For obvious reasons)...
Make sure the can is clean and there is no residue of paint or anything else...
Now mark 4 spots where the four bolts are goint to be attached... Those will work as feets...
Now.. Mark equal distance from the bolts on the can...
These lines will be used later to cut the can open...
Mark the spots where the hings will be placed... (you can add the hinges later.. It oy want... Or totally skip the part.. And make it a top open forge...
Now... Drill the needed holes in their intended places and cut along the line to devide the can into two halves...
Add the bolts in their intended places and secure them properly...
Make the large hole for the steel pipe.. Which Will be used for the air vent and supply...
Now if you are planning to have the top lid.. Then attach it also with the hinges...
**I also used few small nuts and bolts to secure the can lid pieces in their places properly...
Step 3: Preparing the Steel Pipe
It's time to prepare the steel pipe.. Which Will be used for the air flow...
Firstly cut enough length of the pipe... And mark the area you want to make the vent...
Then using an angle grinder... Simply cut the slot...
Make sure to check the fitting and the placement...
Step 4: Insulating the Forge With Refractory Cement
It's time to insulate the forge with refractory cement...
For this perticular purpose... I will suggest a 2:1:1 ratio of Sand : Plaster of Paris : White cement...
I added white cement for extra strength and better bonding...
With this ratio.. Make a tight mixture and add some in the can... Add the steel pipe... Make sure to keep the vent cut out at the top...
Cover the whole inside with enough amount of this mixture... Make sure not to cover the vent area...
Also cover the top lid with the same mixture...
I have used two layers of this cement for better coverage....
Step 5: Let the Cement Set
Let the inner concrete set for at least 12 hours before the next step... In this time.. Make sure the cement stayes at its intended position.. And you can re shape it.. If needed...
Step 6: Making the Base for the Forge...
Now... After the forge is done.. It's time to make the base for the forge...
This base is very important for this project.. Because while working with extremely hot metal and coal... We never want the forge to tip over and make a disaster..
So just by making a solid concrete base... We can easily solve that issue...
For this purpose... I have mixed 1:1 ratio of sand and cement... Don't add too much water in this mixture... We want a tight mixture...
Then filled a small bucket with the mixture and shaped the sides... You can use anything you have handy as the mould...
Make sure the can is well secured in the concrete.. And the 4 bolts from the can.. Will Be the perfect anchor point for the concrete...
After the concrete has been poured... Let it set for at least 20 hours...
Step 7: Finishing the Base
When the concrete is dried well.. It's time to demould it.. And finish the sides.. For that. I simply used my random orbital sander with a 60 grit sandpaper and removed the sharp and extra edges....
Later I used some extra sand paper and hand sanded some hard to reach areas...
Step 8: Painting The. Forge...
Its an optional but a recommend step...
I spray painted the whole forge in. Black paint... This will not only make the forge look good... But also... It will make the concrete a bit weather proof...
But you can skip this step.. If you want...
Step 9: Making the Air Blower...
For my project... I designed a centrifugal air blower in fusion 360..and then simply printed the files with PLA plastic...
I know that I should have gone with PETG.. But I didn't have any... So.....
If someone want... I can give the files for free... But do make sure that you have the exact same dc motor I have used if you are using my files...
I printed all the parts...
Sanded the pieces...
Attached the motor...
Attached the rotor blade...
Closed the blower with intended nuts and bolts...
Attached the adapter...
I also used a 12 volt to 6 volt step down converter.. For the motor... You can also use a DC voltage regulator... For controlling the motor speed.. For my application.. It's enough...
*you can always use a pre-made air blower from online... Which Will be better option for many of you...
Step 10: Connection the Forge With the Blower...
I have used a flexible water drain pipe for my application... And used 3d printed adapters for the job...
One thing I should mention here.. That I have used some m-seal for attaching the adapter with the steel rod... Just to be safe from melting the piece from the radiating heat from the pipe... (It might not be an issue.. But I didn't took any risks)
Step 11: And It's Done...
Our Micro Coal Forge is ready to be used for some small projects... Just load some coal or charcoal pieces and use some lighter gas or a blow torch to light up the forge... Turn on the blower and soon... It will be ready to be used...
Be very careful while using this forge... Use it in a open space... Because from burning coal.. It will release carbon monoxide gas.. Which is poisonous for health...
***
I wanted to show the forge in working state... But.. Unfortunately... It's raining continuously for last few days... And i can't go outside to fire up this forge right now... I'm adding demo pictures now... Will update as soon as possible...
Also I don't have proper metal working tools right now... I do have some basic tools... But I also need an anvil... Pair or grip tongs... And many more.... I will try to collect those as well... And make something with the help of this forge...
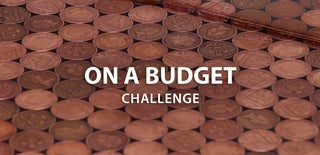
Participated in the
On a Budget Challenge
2 Comments
7 months ago
This might be good for casting zinc parts too as the heat required is not too high.
8 months ago
Nice conception👌👌❤️❤️