Introduction: Backyard Truss Bridge
During tenth grade Physics class I teach mechanics. A main topic of mechanics is the beauty of math in designing buildings, and this is a great project for that purpose. Our goal is to calculate a truss beam through the graphical method of the polygon law of forces. But this time a surprise was there waiting for the students...
Supplies
I designed this bridge big enough to well motivate students, but it had also to be moved on site after a short hike, and also posed over a real river! For those reasons I chose very good quality wood, to reduce size and weight. Wood boards are made by strong plywood designed for buildings. I managed to buy big boards and cut them into smaller rods, about 2cm x 6cm section, 90 cm long. I also bought nine threaded steel rods and 16 bolts with washers and nuts. Of course number of bars and bolts depends by length and number of elements of the bridge.
Step 1: Design
I designed the bridge by hand with simple drawings, but lately I also made a 3D drawing to better explain the project in this instructable. The 3D drawing shows a smaller size version of the bridge, but of course the scheme is repeating every two steps in the middle section. Distance between steps, width and height are all about 90cm long. My bridge has nine horizontal trasversal elements, and it was designed to keep at least three students safely in the middle (most depends by wood quality and good assembly).
You can easily see the assembly scheme in the 3D drawing. Pay attention to connection order of rods, since there are not many possibilities to assemble it so that everything stays aligned.
Step 2: Wood Rods
In the first picture you can see all the longitudinal horizontal and oblique rods, 90cm long, 25mm thick, with 11mm diameter holes at a distance of 35mm from extremity.
The second image shows how we could glue four wood rods around metal bars (two on the sides, one on the top, one below), leaving 10cm threaded rod outside at each extremity.
On the third pictures are five of the nine trasversal boards completed with non-slip tape.
In last picture you can notice there are two additional small square blocks, that extend one rod at about 4cm per side. That is needed because of the geometry of the full structure, to keep every rod aligned and perfectly perpendicular to the traverses.
Step 3: Bolts, Nuts and Washers
You need very thick washers, as to obtain an optimum resistance to loads you will need to tighten every nut and bolt at maximum. My washers are 3mm thick, don't save money on those. In the 3D drawing you see that some bolts are shorter, i.e. the four at extremities, I decided to mark them with white paint to avoid mistakes.
Step 4: Diagonals
When the bridge is very long, more than 7m in my case, it becomes very unstable in horizontal direction, left-right to understand, and you can totally solve that issue with a steel cable stretched diagonally between bolts, as in the drawing. Best option is to to keep the same direction up to half length and then change direction, but it works quite well also with the first easiest solution (see 3D view from top).
Step 5: Some Assembling Details
You can see here some details of the assembled structure. Nothing peculiar other than what already said. You can well see the disposal of the diagonal and horizontal rods, when connected on the bolts.
Step 6: Testing
When the bridge is fully assembled, check every bolt is very tighten, place four supports under bridge ends, and climb on it. We tested the bridge with five adults, and after the first vertical settlement of one centimeter, it practically had only a few millimeters of movement when loaded, really impressive strength.
Step 7: The Adventure
After the initial astonishment for the surprise students carried all rods down to the river, and they assembled the bridge on the bank. It wasn't much easy on the rough terrain, but the bridge was fully assembled in half an hour. At the end, meanwhile some students were keeping it lifted, other students tightened all bolts and nuts. The bridge weight is about 70 kilos, so it can be easily posed on the other bank with the help of a rope and a pulley. Paying attention to any distress by the structure, we hazarded to cross it all together to take a class picture. Water was however no deep and there was no real danger. Everybody survived! But...
Step 8: The Fright!
If you look closely at the class picture you'll see that a student (Pietro you're famous now!) leaned against the top handrail of the truss beam... very dangerous action actually! ...(my fault we didn't discussed it before) yes, since there were an axial compression force of 400 or more kilograms on that beam, which is seven meters long and very thin, so any small transverse push could collapse the entire structure! Indeed the bridge made a loud cracking sound (!!!) and everybody suddenly escaped out from the sides! Then we took a last shot on the bridge, but you see nobody ventured again to reach the central section! 😅
Step 9: Other Solution
Here you can see another optimal solution, where two additional small blocks are not used, and the real improvement is that horizontal top beams are adjacent each other, which is much better for stability. The inappropriateness is that rods are not all well aligned (see top view). Just to try...
Hope you'll make too a similar bridge with your sons, or students, or friends! Math is life!
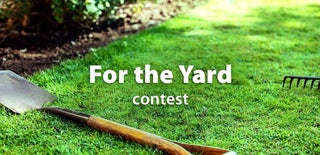
This is an entry in the
For the Yard
12 Comments
1 day ago on Step 2
Beautiful! I need one of these over my creek but it has to be able to hold up a riding mower so I can clear all the (expletive deleted) grass and weeds on my property on the other side of the creek.
Reply 1 day ago
I think you could make it, it should hold about 300-400 kg, right? Just don't risk your life!
Reply 9 hours ago
Would an understructure (reversed truss) below the 'deck' level help the bearing load for the riding mower?
Reply 1 hour ago
YES! Thanks to remembered it to me, I could add a detail.
The handrail is very long and compressed, which makes it unstable, but if you reverse up-down the bridge that truss will be taut and totally stable. probably the load could double.
Reply 2 hours ago
Totally doable. Figure out the weight of your machine, then literally go times 10 as a safety factor. Build from there. 4x4's would absolutely do it. You'd just have to move to larger fasteners or a higher shear strength component.
1 day ago
We did something similar (although much smaller) in physics class when I was in the tenth grade (maybe).. Only difference is that we used balsa and there were more than 10 bridges to test. Each student had 120 inches of balsa stick to design and build a bridge 18 inches long. We were only allowed to use wood glue for assembly. The triangle designs held quite a bit more than I was expecting.
Reply 1 day ago
eh eh, glad you still remember it!
1 day ago
This really is super cool. My favourite instructable so far (though I guess I’m only about a six month member).
Such a practical skill/tool to solve real-world problems that I’ve run into myself more than once.
Thanks for this.
1 day ago on Step 4
Hi. Great project!
It looks like in step4, the 3D image has the same drawing twice.
Reply 1 day ago
nope, you've to look diagonals ;)
2 days ago
Amazing class work to put math out in the real world! Bravo!
I think I understand Step 9. It might be good to have close ups of the 3D images of the joints side by side to help understand what was changed.
Was the bridge disassembled and saved for next year?
It might also be nice to have one or two steps sharing the math.
[With a few additions this would have been a great entry in the Project Based Learning Contest]
Thanks for sharing an impressive project!
Reply 2 days ago
Unfortunately that contest is open to US teachers only...
Yes the bridge is now disassembled, and with some luck will be another surprise fox next 10th grade students.
About step 9 it's only a hint to give something to think about.
The math behind this project is really amazingly beautiful, it's all about forces, vectors and polygons, all geometrical with no calculations! There are probably great math teachers which could explain it better that what i could do with a more practical instructable... and I want teachers discover by themselves the beauty of this process.
I'm happy you liked the project! Best wishes!