Introduction: Micro Brass Trefoil Knot Using Knee Mill
Project introduction: Around 2015 I came across a video by YouTube user Pocket83 (https://youtu.be/Jw1Eyu54whI) showing how to make a trefoil knot from a solid piece of wood. I had tried several times from a block of mahogany, but unfortunately my chiselling skills suck and I kept on cracking it. Finally, I tried one final time and came close to finishing, but I eventually got bored waiting for some carving burrs to arrive from China and moved on.
More recently, I decided to start a project that would expand my skills with a Bridgeport-style knee mill while producing an attractive final result. Thus, the idea of the cubic trefoil knot in brass was born. Unfortunately, brass is quite expensive and making a large knot from a solid cube would cost far too much. I therefore chose to make this knot very small - less than 1" face to face. From start to finish, it took around two years with numerous failures and setbacks. I describe these at the end of the project, so you can get an idea of what does not work.
Working with metal makes some parts of the project a bit easier to do, especially with the use of a knee mill, but metal has its own challenges. Work holding is much more important, feed rates and rotation speeds come into play, and the precision goes up by an order of magnitude. Finishing is also more time-consuming and requires a fine eye for detail.
If you don’t have some of the equipment listed here, please still read on – where possible, I’ve tried to include alternative tools that you can use and still get decent results. The only critical nonstandard tool, in my experience, is a screwless vise. As I will detail below, using a standard vise makes it quite difficult to hold onto the part in later stages. I suppose you could mill custom soft jaws instead, but that seems like too much work for me (especially as I intend to make more complex knots in the future, which would mean making a set for each type). Instructables user Steamcheng also suggests cutting aluminum "filler" blocks to fill the cavity and support the part in a standard vise, though I have not tried that myself.
Unfortunately, I didn't take many pictures during the final build (though I took many photos during prior attempts, and I have used those where appropriate). Where necessary, I have supplemented the text with screenshots of a 3D model.
Supplies
Materials
Brass bar stock (3/4” in this example) or preformed brass cube (if you know where I can get these, let me know!)
Sandpaper to 2000+ grit
Stainless steel tumbling pins or other tumbling media
Layout fluid (Dykem) (optional)
Tools
Milling machine (I used a manual knee mill, so if you use a CNC machine some of the advice I give will be redundant)
Milling accessories: parallels, edge finder, toolmaker’s screwless vise
Milling tools: facing mill or fly cutter, appropriately-sized end mill (3/32” used here), roughing end mill (optional, not shown, see step 4 for information)
Measuring equipment: precision granite block (optional for layout), calipers or micrometers, height gauge (optional for layout), Z-presetting tool (optional)
Jeweler's coping saw
Jeweler's files (assorted shapes, particularly flat and square)
Loupe or other magnification
Vibratory tumbler
Step 1: Make or Obtain Brass Cube
Since we’ll be dividing the cube into a grid of 7x7x7, I started by choosing a final cube size that was easy to divide into 7 parts. I stated with 3/4" square bar which I then trimmed to 0.7". Each unit is therefore 0.1” (though I used a 3/32” end mill, so the final product is slightly imperfectly sized). It would be slightly easier to start with 1" square stock, trim to 7/8", then use a 1/8" end mill.
I used This Old Tony’s method (https://youtu.be/tW8HNAlUXxU) for making square stock; if you don’t want to watch the video I will summarise it briefly. Begin by facing off one side, taking off only enough to remove the factory surface. Deburr the edges and rotate that side so that it is against the fixed jaw of your vise. Face off the other two sides, deburring before replacing the stock in the vise. Then, cut the final 3 faces to size, taking passes and measuring frequently until the cube is the correct size.
Do note that the edges of the cube will be quite sharp before deburring. Handle with care.
Step 2: Pattern and Geometry
This pattern comes directly from Pocket83’s original video (https://youtu.be/Jw1Eyu54whI), and gives a good idea of what needs to be removed from the stock in order to get close to the final shape. There are some important pieces of information missing, because they can’t be fully shown in a 2D projection, but as more and more material is removed, it becomes easier to see what needs to come off without referencing the pattern. I recommend watching Pocket83's video so you get a rough idea of how the pattern relates to the geometry.
I used this pattern for reference when orienting the stock; since you will need to reorient the part frequently, it is very easy to become confused. Personally, I see the pattern as a face with two “eyes'' and a “smile.” I will use this analogy in step 4 for roughing, but ultimately the “eyes” and “smile” are only used for reference (as opposed to being drilled out as in Pocket83’s video).
I also 3D printed a model at 2X scale before starting. I kept it nearby to ensure that the geometry was correct throughout.
Step 3: Pattern Layout
Brass is soft and marks easily, but I still used marking compound (Dykem) for visibility. Using the height gauge and granite block, scribe out the grid in 0.1” increments on all 6 faces. If you don’t have a height gauge and granite block, you can use calipers, but be aware that the result won’t be as accurate. Once you’ve marked out the grid, transfer the pattern to at least three faces (I used the height gauge to mark out the center of the appropriate squares, but you can always scratch it out with a scribe if you prefer – these markings are purely for reference).
You can also transfer the pattern to the faces using a toner-transfer or other marking method. Having even a very rough and imperfect pattern is better than having no pattern at all - as the cube will constantly be rotated during milling, it's easy to lose track and make incorrect cuts.
Step 4: Rough Milling
Note: the photo shown was from an earlier iteration, which is why it has holes in it. I later abandoned the idea of pre-drilling, so feel free to ignore them. I explain more about earlier versions in the last step.
This step is incredibly repetitive when done on a manual milling machine, and it’s easy to get confused. The general idea is to locate the edge of the part, locate the top of the part, identify the coordinates of the desired end of the cut, then turn the hand wheels until the tool is where you want it to be. I will go through the process for one set of cuts, and the rest are all the same.
The first set of cuts are 2 unit x 2 unit through cuts. Each side gets three such cuts: I see them as the “ears” and “hair” in the smiling face analogy. I kept my depth of cut to 1x the tool diameter and my stepover around 1/2x the tool diameter. Although accuracy is not super critical with a decorative project, I still measured the dimensions frequently as I approached the target size.
To start with, I chose the front-top-right corner as my zero point. Set the RPM to low (<1kRPM), load the edge finder, turn on the spindle, and locate the edge. Then, offset the tool by 1/2x the diameter of the edge finder (in my case, the edge finder is 0.2" diameter, so I offset by 0.1"). Zero the appropriate axis and repeat. Note that by doing so, you are locating the centerline of the spindle relative to the part.
Then, load the tool. There are a number of ways to locate the Z zero (feelers, paper, dial presetter, etc) but I just very slowly lowered the tool and moved it back and forth over the corner until the cut began. I then backed the tool off 0.001" and set the Z zero.
In the attached diagram, you will see that I have included the actual location of the edge as the primary dimension, and the location of the centerline of the tool in brackets. If I move the centerline of the tool to the location in brackets, the edge of the tool will be at the desired location. To come up with these values, I either added or subtracted the radius of the tool from the target location.
Begin taking the first cut. Since the tool is small, I took a series of passes from front to back, keeping the X axis constant and raising the Z axis after each pass. Then, I moved the X axis over and repeated. If you prefer, you can always use a larger end mill for this step, which would result in fewer passes.
In each orientation, you can do three cuts: two cuts from the front, and one cut from the side. After that you will need to remove the part from the vise and rotate it.
Step 5: Finish Milling
As before, locating the edge of the tool accurately means offsetting the tool by 1x radius of the tool. To keep track of the target numbers, I made a list of where the tool needed to stop at each stage of cutting.
Since I didn’t want to have to keep a random 3-digit number in my head throughout the whole cut, I simply lifted my tool above the workpiece, moved it to the target position, then reset my X and Y zero. That way, I only had to move the tool until the DRO was zeroed out.
The finish milling step actually consists of 14 sub-operations – two operations for each of the six faces of the cube, plus two operations to remove the center block of material. In each orientation, a 4x2x2 block (shown in dark blue) is first removed from the front, then a 1x2x2 slot (shown in magenta) is carved towards the back of the workpiece. Typically, having engagement on both sides of the cutting tool is not recommended, but the material is soft and the tool is small so I didn’t have any issues unless I overfed it.
If you have been using a normal vise up to this point, you will need to switch to the screwless vise at some point during these operations. I was still able to hold the part on the edge of the screwless vise without losing grip, though I did need to pay attention to which of the slots I was using (so that I wasn’t at the end of travel of the screw) and that I manually squeezed the jaws together before tightening. When I tried to hold the part in the same position in a regular vise, the jaws did not remain parallel and therefore grip was greatly reduced. Having a screw less vise serves two purposes: first, the jaws are much narrower, so when the part is secured at the edge, the torque on the jaws is much smaller. Second, the screw less vise applies force downward as well as inward.
Once you have removed the blocks, you will be left with a 2x2x2 cube in the middle (shown in yellow) and six supporting members. Remove the cube using the mill. It may be possible to remove the supporting members with a long enough tool, however I simply decided to remove them with a jeweller’s saw (see next step for detail).
If you would like to save time filing, you can also clean up any radii left by the tool (for example, in cutting the last 1x2x2 slots) however I chose to file those sharp corners by hand.
Step 6: Hand Tools
Start by removing the remaining supporting blocks (shown in dark green) with a jeweller’s saw. You will need to carefully thread the blade through the holes in the block and get creative with your workholding and sawing angles to do this. I used a handheld two-jaw vise to hold the workpiece, but instead of holding it by hand I mounted it in a ball vise. In this way, I had access to a larger area around the part (because the jaws on the handheld vise are smaller and therefore don’t get in the way as much) but still had stability and flexibility from the ball vise.
Once the part is in its final shape, you will need to move onto filing and polishing. If there are any radiuses left from the tool on inside corners, you can use a square file to make them sharp. If there are any misalignments created through measurement or handling errors in machining (very likely), you will also need to even them out. There will, of course, be marring from the blade of the jeweller’s saw if you used one as well.
When filing, it’s easier to remain straight if you have a straight line in the near background that you can sight against. The jaws of the handheld vise are not perfectly flat, so I used a small cutting mat with a nice reference grid. This way, I could check the position of the file and the shape of the workpiece against a known straight line and avoid accidentally filing a taper or curve. Take your time and check your work often.
Step 7: Finishing and Polishing
This step can take many forms, and it depends on what kinds of equipment you have available. I only had sandpaper and a vibratory tumbler, so I decided to start by sanding up to 2000 grit using DIY sanding strips then tumble with steel pins.
The sanding bars were made by laser-cutting tiny tapered bars from 1/8” acrylic (each bar was cut less than 0.1” wide) then supergluing strips of sandpaper to the tapered end and trimming to size. In all I made around 70 individual sticks. As usual, sand each face until the marks from the previous stage of sanding have ben removed.
Since the finish will be shiny and slightly irregular, tumble the knot with stainless pins (available at hunting/firearm stores) for 3 hours, checking every 45 minutes to make sure you don't over-tumble. Finally, I cleaned the knot in an ultrasonic cleaner. If you don't have an ultrasonic cleaner, you can always manually clean it with a Q-tip. Do note, however, that standard Q-tips are slightly larger in diameter than the gaps between individual members, so you will need to peel off some of the fuzz to make it fit.
Finally, the knot is complete. I estimate that the final version took around 40 hours start to finish.
Step 8: Approaches That Didn't Work
As I mentioned in the introduction, I tried numerous approaches that ended up not being successful. I am documenting them here in case you feel inspired to modify my approach; the only way I was able to finish this project was by exhaustively trying out everything that didn't work until I figured out what did.
The biggest problem ended up being how to hold onto the part; with a standard machining vise, the workholding becomes very difficult in the end stages. In particular, the gripping surface becomes L-shaped if you try to grip in the middle.I tried gripping the part from the edges of the vise, but that kicked the jaws askew and greatly reduced the grip on the part. 3D printed soft jaws didn’t help.
Since I did not know about the screwless vise until much later, I initially tried to do a bunch of processing by hand. I would rough out the majority of the material needed until I could no longer securely hold the part, then clumsily hack at it with jeweller’s saws, handheld rotary tools, and miniature watchmaker’s files. I came close to finishing several times, but the process was incredibly tedious and labour-intensive, and I inevitably ended up filing a curve or taper into one of the members or making one segment thinner than the rest.
In terms of milling strategy, I first tried to imitate Pocket83’s geometric approach. I either drilled or milled out the “smiling” pattern, followed by 2 unit x 2 unit through cuts as seen in Step 4. As it turns out, drilling holes that have a depth that’s 7-8x the diameter of the drill is quite hard because the tool gets gummed up with chips and wanders like a drunken sailor. I finally succeeded by first spot-drilling 48 times (8 spots per face x 6 faces) then drilling from both sides. As you can imagine, this took an eternity and didn’t really help me at all in the end.
Eventually, I realised that I was using a piece of precision equipment (as opposed to the relatively coarse woodworking tools used by Pocket83) and could therefore do whatever the heck I wanted, including milling blind slots and steps (rather than mostly through cuts). Nevertheless, I consider these side expeditions to be valuable because they taught me skills that I wouldn’t have picked up otherwise.
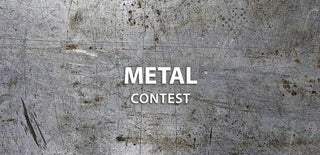
First Prize in the
Metal Contest
6 Comments
5 weeks ago on Step 8
what about rosies metal
melts at 70c
cast it around mill melt in hot water turn re cast it mill ect ?
7 months ago
By the way, I added a few interesting photos in steps 6 and 7 showing the jeweler's saw, rough filing, and finishing.
7 months ago
You mention problems with maintaining perception of which face is which.
Perhaps begin by marking each face with an orientation arrow in a different colour ?
(Both on the the plan and on the workpiece.)
Then you can always see exactly which way round it is, and relate it to the plan.
Reply 7 months ago
Certainly, there are many ways to improve one's perception of the shape. Since this perception is very individual, it's good to come up with a few different techniques to try out. You may notice in one of the pictures that I used multi coloured permanent marker instead of Dykem, just to help align with the template from Pocket83.
Personally, step 4 was the most difficult for me. Once I successfully completed it, the orientation always became very obvious. Of course, other people might find that they don't see the shape clearly until later on.
Tip 7 months ago on Step 8
For workholding shapes like that, I find it helpful to use aluminum "fill blocks" to fill in the voids on the object so it can be held square and tight in the vise after removing various sections. Just mill out a piece of aluminum to fit in the spaces and clamp solid in the vise. You can even mill out part of the aluminum if it is in the way of a cut with no problem.
Reply 7 months ago
That's a good suggestion, and would definitely save money on a screw less vise. Made perfectly to size, they would be difficult to align at this scale, but I think that it would still work even if it's oversized in at least one dimension.