Introduction: My ‘Light’ Engine Locomotive – a Unique Scrap Metal Train Lamp & Bridge
Recently, my wife asked me to make a nice SIMPLE lamp for the lounge. “No problem” I said. Several weeks later I’d built a detailed, scrap metal model of a locomotive complete with coal wagon and a 4ft long, wall-mounted railway bridge for it to sit on. I’m not a huge fan of trains, and I’d ignored the initial design brief almost entirely, but the wife and I both love the end result and it’s a real one-off that I hope you’ll enjoy too.
The basis of the train is an old, empty gas cylinder that I'd kept because I’d always thought it would make for a great train engine given its size and shape (I hoard scrap metal like it’s gold!) The opportunity to make a lamp was just the excuse I needed to finally repurpose it and put it to good use.
Supplies
To make this, the main materials you’ll need are:
- A good collection of scrap metal including:
- An old metal cylinder – mine was a disposable MIG welding CO2 cylinder (for the train engine)
- Cogs from old hand drills and several tap/faucet handles (for the wheels)
- Bits of old ‘box section’ steel (for the body/chassis)
- An old bread baking tin (for the coal wagon)
- Some steel sheet
- 5v LED 'warm white' strip lights – about 70cm/30” long.
- 2 x LED lights, 2 x on/off switches, and some 1mm electrical cable
- Chicken wire approx. 50cm x 50cm (20” x 20”)
- An empty plastic bottle
As for tools, I’ve assumed most people tackling this have access to basic tools and so the key, additional tools required include:
- An angle grinder with 1mm cutting discs and flap discs
- A vice
- A welder (I used MIG)
- A router or chop saw (for cutting the sleepers on the wooden bridge)
- An electric drill
- A soldering iron
Step 1: Full Steam Ahead
I spent a lot of time on Pinterest looking at different trains and hadn’t appreciated just how many different locomotives there were back in the day. Eventually, I opted to use a Central Pacific Railroad #60 Locomotive as the basis of my lamp as it had lots of great features that I thought I could incorporate into my design, including a huge chimney/smokestack. Check out this beauty (train photo courtesy of Wikipedia). Now I had a rough idea of what I wanted to make, I started to rummage through my treasure trove of scrap metal.
Step 2: Do the Locomotion
I sat the cylinder (aka the ‘boiler’ or 'engine') on a couple of lengths of box section to get an idea where the main parts of the locomotive should be positioned. I used different photos of the train above to get an idea of the scale of the main parts of the train relative to each other. It's worth noting at this point that I’ve not measured or drawn anything before starting assembly. I don’t tend to draw things out when I’m making like this as I’m guided by the scrap metal I have lying around me rather than trying to stick rigidly to a design. All of the dimensions were ‘eye-balled’ rather than measured which helps to keep the project progressing rather than trying to get every part sized to an exact scale. Personally, I think it adds a bit of character to the whole thing this way. You can see how I put a few parts together loosely to get an idea of the end result before I started welding or adding any of the finer details.
Step 3: On the Right Track
Without further ado it was time to start cutting and welding. I’ve detailed the main steps of the build in order of construction as follows:
The boiler – the old gas cylinder to gives the whole piece its distinctive locomotive shape and raw, metal colouring. Stripping the paint off this thing was a nightmare though. A combination of paint stripper, sand paper, and flap discs eventually got through it all but it was a messy, labour intensive process. The empty cylinder was cut and welded onto the two parallel pieces of box-section as per the mock-up described above. These form the support for the front wheels. At the back, a short piece of rectangular box section welded to the underside of the cylinder forms the rear base of the train and provides a mounting point for the cabin and rear wheels. I should add that the cylinder was fully emptied before any cuts were made and also, as it contained an inert gas (CO2), there was no fire risk when cutting the empty cylinder with the grinder. To be sure any cylinder you use is empty, you may consider filling it completely with water to force any residual gas out.
Wheels and axels – Threaded rod welded onto the train chassis form the axels for the front wheels. The wheels, made from tap/faucet handles then fit onto these and are held in place with a small nut. The rear wheels, however, are bolted directly to the chassis as I had some bolts that fitted through the wheels perfectly. Before I cut or welded anything at this stage, I checked to ensure the wheels wouldn’t foul each other once they were fitted and that they all touched the ground and would align properly when the train was on a flat surface.
The beauty of using old hand drills for the rear wheels is that they already have threaded holes in the cogs which are in the perfect place for mounting the locomotive’s connecting rods to the pistons. The connecting rods themselves were made from brass bar which I filed down by hand to give a more realistic looking shape and the pistons that the connecting rods join to were made from old sockets.
The cabin - The three sides of the cabin are made from a single sheet of steel. The windows were cut out carefully using a thin (1mm) cutting disc to cut the edges and then a hacksaw blade to finish the corners. I then bent the sheet in the vice to form the 3 sides. The roof was a longer piece of sheet which I then bent around a paint tin to give it a subtle curve and it was then cut to size.
The plough – this was made from sheet steel cut into strips. I started with the bottom, angled piece held in a vice and then tac welded smaller strips in place and gently bent them so that they all aligned before welding on the flat piece at the top. The keen-eyed amongst you will spot two different versions in the pictures. The first one I built was too big… eye-balling dimensions doesn’t always pay off! Plus, I didn’t like the fact I could see the welds on the front of the plough, so in the second version I made sure I welded the strips onto the back of the plough. Nothing quite like trial and error to refine a design! :)
Brass handrail - I cut threads into some short lengths of brass bar and then screwed these into steel nuts that I’d welded on the side of the engine. I did this as brass won’t weld or solder to steel easily so I had to think of a way of fixing the two different metals together. With the uprights all in place I then soldered the longer, horizontal brass bar across the top on each side.
The wagon – this was an old bread baking tin which I added wheels to in a similar fashion to how I’d mounted the front wheels to the train. I made sure I’d finished both the train and the wagon before attaching them to each other. The coupling that connects them was made by welding the end an old spanner to each piece.
Step 4: Planning a Route
With the train built, it was time to start planning the lighting. I have two circuits on mine – a switched circuit for the smoke, and a switched circuit for the cabin and headlight. The wiring was quite straightforward, but I’ve included a simple wiring diagram to help you out. In terms of routing the cables, this was also fairly simple: As the gas canister is hollow, it’s easy to conceal the cables and run them through the inside of the train. The cables then feed through a hole in the floor of the cabin, run under the train, cross over to under the wagon and then go up into the housing for the switches. My tip here is to make sure you use grommets, heat shrink and/or electrical tape to prevent the cables coming into contact with any sharp metal edges along the way. Black heat shrink and tape also helped to disguise the bright colour of the wiring.
For the lights, I opted for low voltage (5v) LED lights to make the whole thing that little bit safer and easier to wire up. Also LED lights give off very little heat which is essential for something that's going to be wrapped inside a fabric blanket.
The lamp is powered from mains electricity but the whole thing could have just as easily have been run off of batteries as the lights are low power and the wagon would have been a great place to conceal a battery pack. I wanted mains power however as this lamp is to be fixed in one place. I used warm white LEDs but you could use any colour you want and there are plenty of options for colour changing versions if that’s your thing.
Next up was the switch box. I spent way too much time on this given it’s not even visible in the train’s final position! You could save yourself some time by using a pre-made, purpose built box. Mine was made from a piece of thin walled, steel box section with a hole drilled out through the bottom and then a bigger, square hole cut out of the top. It was then welded inside the coal wagon. The switches (salvaged from an old power tool) were screwed into a 2mm thick piece of brass and, once wired up, the brass plate was screwed to the top of the metal box. The wires enter and exit through the hole in the bottom of the box which goes right through the bottom of the coal wagon too.
Step 5: Light Railway
This step focusses on making the ‘smoke’ and positioning the LEDs to form the lights on the train. Note the first few pictures are a mock up model I made to help detail the process more clearly. On the final version, a thicker fabric was used instead. There are additional notes on the photos to help you out here too.
The smoke from the steam engine is made from the material inside an old quilt wrapped around some chicken wire.
Firstly, I rolled the chicken wire into a rough funnel shape and then welded it (carefully) inside the top of the chimney/smokestack. This took several attempts as it’s very easy to melt through the thin gauge wire. I left a small gap between the inside edge of the 'chimney' and the chicken wire so that I could tuck the ‘smoke’ cloth down into the chimney to give it a neat finish. At this point, make sure any rough edges and burrs are sanded off so that they don’t damage your wiring… or fingers. With the funnel wire now fixed in place, I gently squashed and manipulated it into a more natural shape; a gentle flow backwards to give the impression that the train is moving forward. From there it was time to solder in the LED strip lighting, but do make sure you let any welding cool off before you start pulling cables through the chimney.
To prevent the LED strip lights from shorting out on the metal chicken wire, I put the whole strip inside a plastic drinks bottle (with the bottom chopped off to get the height I wanted). The bottle protects the LEDs but also helps to support the strip lights and keep them upright. I used a transparent bottle so it didn’t impact on the colour or intensity of the light output. Once all this was in place, small zip ties were used in various points around the chicken wire to help hold its shape.
The old quilt fabric was cut into a long, ~4" wide strip which I wrapped round the chicken wire starting at the bottom of the funnel and working upwards. I then tied thin, cotton thread around the fabric at the bottom of the funnel to hold it in place. Following a similar route to the fabric, bottom to top, I wound the thread around the funnel too. A final knot in the thread at the top held the fabric in place. In the pictures you'll see I've used a mock-up model with fabric and thread that have contrasting colours so you can easily see where the thread was placed. On the train itself, both the fabric and thread used were white and so the pictures would not have shown this process as clearly. The fabric used on the train smoke was also thicker, and fluffier than that used in the mock up and so that naturally gave it a great smoke plume effect.
Don’t worry about making the fabric too neat, the material should look a bit rough in places and overlap on the edges as it adds to the smoke effect. Just make sure it hides all of the chicken wire. Any excess can easily be trimmed off if needed.
Single LEDs were used for each of the other two lights – one for inside the cabin which was hot glued into the middle of the roof. Another was then mounted inside a large steel nut at the front of the train to form the headlight. The light it emitted was too bright so I cut out a piece of plastic from a milk bottle and pushed it just inside the nut to help soften the light. The threads of the nut held the plastic in place perfectly.
The wiring was soldered to the LEDs and switches and then all plugged in to test.
Step 6: One Track Mind
So finally, how to mount this thing. By this point I was happy with how it looked. I could’ve sat it on a shelf and called it finished… but nope, I started wondering what else I could do to really make it a statement piece in our lounge and so, naturally, I built a bridge and rail track for it to sit on.
The bridge was made by firstly measuring the space I had between the walls of our alcove (4ft/1.2m), then cutting a couple of lengths of box section steel to match. These were braced with some sheet steel offcuts to keep them parallel and straight. The supporting legs were made in a similar fashion and welded on at right angles to the bridge. The arches were formed by bending lengths of 10mm re-bar over my knee, bending it bit by bit along its length to the shape I wanted. A top tip when bending metal is to bend it before you cut it to length. This is because it is almost impossible to bend the very ends of a piece of metal, especially when only using limbs instead of proper bending tools! So get the right shape first, then cut. With the arches then welded in place, the uprights were cut and welded individually, maintaining an equal spacing between each one. Ok, ok, I’ll admit I did actually do some measuring for that bit.
The wooden railroad was made from a single piece of pine scaffold board which I cleaned and sanded first. To give the effect of the railroad supports looking like individual railroad sleepers, I routered a recess along the bottom edge of the board so that the sleepers then sat proud of the wood below. Using a chop saw, I then cut equally spaced, horizontal slots along the full length of the board giving the illusion that each sleeper is a separate piece. The track itself was made from square steel bar which sits atop the sleepers and, perhaps obviously, the track was made to suit the width of the train so that the wheels would sit on top nicely. The wood was then stained with a dark oak wood stain.
To finish I used cable tacks to route the cable along the far side of the bridge, (out of sight), down the wall and into the power supply which came with the LED strip lights I bought.
Step 7: The End of the Line
Once it was all in position, it was great to flick the switches and watch it light up. It was a fun build and the novelty of having it on display in our lounge hasn't worn off yet. As a lamp, it functions really well - the smoke lamp lights the whole area up beautifully, but with the smoke switched off, the headlight and cabin light give a more subtle output which really changes the look of the whole thing. By day, the train still draws a lot of attention from friends and family even with the lights switched off. Its proven a hit both as a lamp and as an ornament in its own right.
Well, that’s the end of the line for this project (and my terrible puns). I hope you've enjoyed this instructable and I welcome any comments or questions. Thanks for reading!
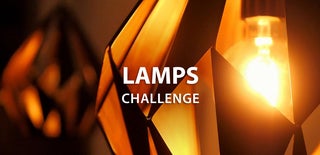
Grand Prize in the
Lamps Challenge
14 Comments
Tip 3 months ago
Hi friends, I think the confusion with the creation of the smoke might be cleared up by explaining the name of the material that was used to stuff the quilt. I'm pretty sure it's universally called "Batting" throughout English speaking countries, but if it is not a quick search of the word will pull up the product and its many uses.
It can also be referred to as "poly fill" or similarly when read on the tags of stuffed toys. The distinct difference (in my quite limited experience on the topic, not a professional just here to help) is that between the two the batting used here can also often be found under upholstery cushioning as a layer between foam couch seats and other similar applications along with being used as filling in comforters. When purchasing new at sewing and craft stores batting most often comes in a roll, as it's produced as a layer of varying widths and thickness.
Poly fill or poly-fil or fiber fill will come in a clump that is intended to pull apart and fit into any sized areas that need plush stuffing. Having just researched further for this post, I see that it's now in 'dark' and which could possibly add dimension to the depths of the smoke clouds.
But, it's likely everyone has a crummy, flat floppy old pillow that should have been tossed ages ago! Here's your perfect opportunity to get this literal Stuff for free! It's washable too, so just give it a squeeze and hang it to dry. I hope this helps everyone who's interested to get started on this most excellent project!
3 months ago
Me when I saw the first picture: HOW DID YOU MAKE AN EXPLOSION SO PERFECT
Me when I saw the next picture: Ohhhhhh ok nvm
5 months ago
Congratulations on winning the Grand Prize!
Reply 5 months ago
Thanks very much!
5 months ago
This is amazing looking. Great work! Thanks for sharing your creativity.
I'm with RobertS854.'s comment, I still don't understand the construction of the smoke.
In Step 5 photo 7 it shows smooth cloth wrapped around chicken wire [Is this just a mockup to show the thread but wasn't used?], Photo 8 looks like smooth fiberfill batting (no cloth, #7,underneath), Photo 9 the cool fluffy billowy smoke. No description is really given as to what happened between each step to get to the next. How did you get the puffy billowy effect? Great effect!!!!!
Reply 5 months ago
Hi, thanks for your comment and sorry I've not been clearer. You're right that the pictures shown are a mock up of the actual version, intended to give more detail around the steps taken on this part of the build. For the actual smoke on the train, the same process was used but with a thicker, fluffier fabric. This naturally gave it that billowy effect you see in the final version. I will update the intractable to highlight the mock-up photos. Thanks for the feedback!
5 months ago
Congratulations on being a finalist in the Lamps Challenge!
5 months ago on Introduction
Chicken wire, cotton thread, old quilt. How is the smoke effect made with these items? I read it 3 times... sorry, I am confused.
Best Answer 5 months ago
Hi and thanks for your question. I've updated that particular step with some additional pictures and detail so hopefully that explains it more clearly now. :)
Answer 5 months ago
OMGoodness, much better. :)
5 months ago
This is fantastic! Congrats!
I would only glue to the wall two figures of tunnels in both sides of the rails. It would seem that the train is going through the walls... :^)
5 months ago
I must say this is really cool and unique metal train lamp & bridge.
5 months ago
Very cool. Just took a welding class myself to learn how to do hobby stuff like this and love that you made this all from scraps. You have inspired me to see what is lurking aroun the workshop to make cool projects from. Nicely Done!
5 months ago
This is so good! I love seeing stuff like this - beautifully done and very inspirational. Thank you for sharing this!